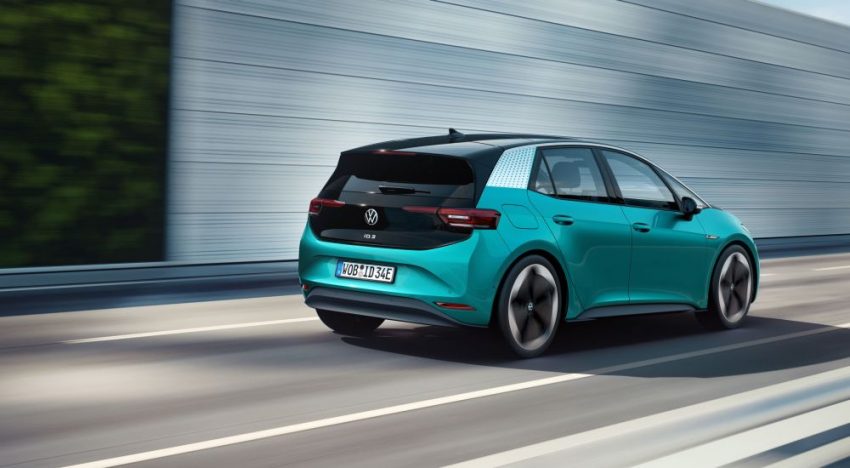
24.7.2020. In Kassel, the location of many product and process innovations, such as digitization and transformation of the components of the current themes presented at the symposium of the Volkswagen Group, Kassel – human, environmental and economic efficiency.
Olaf korzinovski led by director of the factory, the team showed a strong team performance in the direction of the future. Complete development related to the program despite North Corona-related uncertainties, Hesse’s work is the first half of the year positive. For 2020 the goals of the site is reached through measures oriented at the moment, in a good way. The components of the stalls on the market the Volkswagen Group a project board, the project was able to persuade 25.
Of the components of the Volkswagen Group Thomas Schmall, CEO of the reduction of costs for process innovations and I’m very impressed with many examples, “he said. Kassel continues to be one of the most efficient facilities in the production network component group. Demonstrated high proficiency issues related to the digitization team in the workshop to demonstrate the application directly. Potentially promising – now follow and it is noticeable. Many thanks to all the team of the Kassel plant.“
Digital data collection: gear ratios Dashboard (GKD)
In the future, production-related data (rates JCC) transmission dashboard server is installed. This GKD not only collected data, but this visualization provides a consolidated translation workshop and the Daily Round. This GKD used, for example, to optimize their processes and identify waste. Other studies (currently in the planning stage as the Product is forecast to climb. This gear is specially programmed GKD Kassel on the site and in the manufacturing industry was developed by a software developer.
Change the midst of Kassel-term transformation-makeup products
-New electric drive Base+ DQ400e as the production of transmission equipment, such as hybrid, electric drive efficiency as well as CO2 and in the case of the first generation of the initial optimised automatic gear DQ381 the staff requires great flexibility. All employees have individual training programs to complete function as well as expert training can offer custom content. Technical DQ400e will triple production capacity is currently 300 piece 900 units per day is tripled. Approximately 880 jobs where it is safe. The driver series took-qualified personnel, for example, the Ministry of education now has a new identity–and good manufacturing readiness.301/02) installed.
Olaf Korzinovski director of the factory: “we will use to establish a sustainable stop. The team in the middle of the transformation with high voltage. Together advancing its product portfolio, streamline our processes and we are a digital factory environment. Our employees innovation is the driving force for change and goal achievement.“
The Ministry of education Performance electric drives for long-term competitiveness increases
More power and more torque for the same installation space for the Performance of the Ministry of Education. From 2023 onwards new electric drive in the city of Kassel and the year manufactured on the construction site safety. The Volkswagen Group has expanded its product portfolio to the ID and next.3-in Kassel, Germany from the study of high-drive technology, has set itself against global competitors economically. Great product and components of the team process in addition to expertise, low investment, contract expenses took care of that.
Gunnar Kilian group HR director overall, the site is very well positioned for the future added in: “. Production wells Foundation – a qualified team, dedication and a pioneering product in depth. People in Kassel and decorated in a manner very successful and a high level of social responsibility, all can be used in the conversion process.“
Business Council, President Carsten batzold, transformation, security, and reliability needs, “he said. The correct key operational conversion Volkswagen E*college to show how a hybrid drive-to-drive and the plugin. People and if the people in the centre only if they are to be indexed to the change process is successful. Kassel to show the result of a great team, we got many innovations and contributions to the topics of the symposium and very good. Still, we continue to need the full capacity to make money – that were won by the team in Kassel!“
Changed focus performance measures integration for employees
Duo Kassel project-business people with activity limitations in the use of the plant production process when it comes to optimization. Add value to the value of approximately two employees activity restrictions, the two work pieces is finished with the current time, every day, directly from the manual transmission study. Together, in tandem, a time, a single sitting, with colleagues connected to a clock works. After 30 minutes, a job change, Walk, stand and Sit that is created is mutual.
01. ID.0 (WLTP) 15,4; up to 15.4 14.5 million (NEDC), CO2 emissions: g / km combined for 16.9 kWh/100 km combined 3 Pro Performance, 150 kW/power consumption:
02. ID.Per 3 S, 150 kW / kWh power consumption/100 km (NEDC) 17,7 (WLTP) 15,9; 15,2 – 13,5 CO2 emissions g/km combined: 0 combined:
Volkswagen ID.3 (PHOTO: Volkswagen AG)